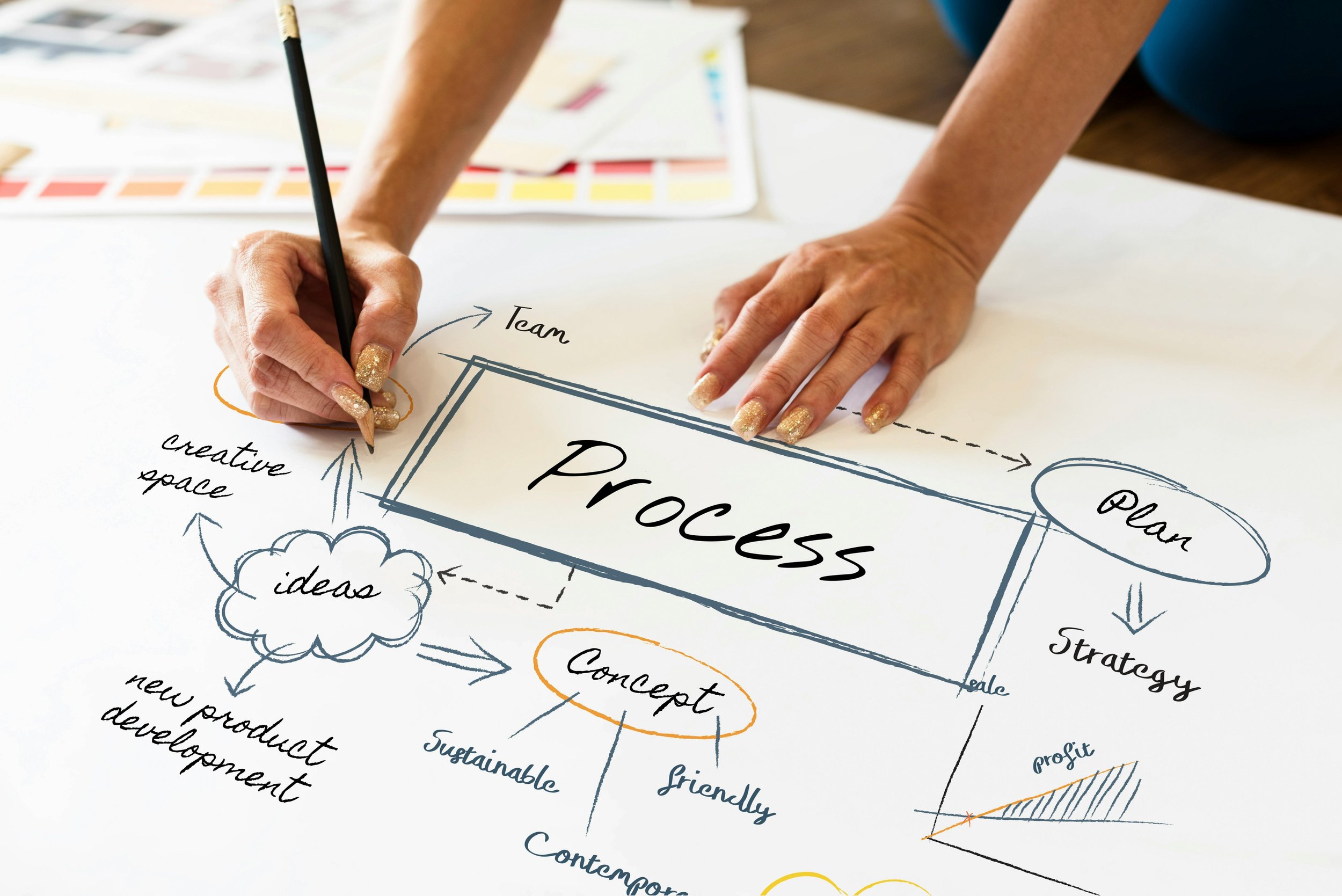
Eliminate Waste. Achieve Excellence.
Lean & Six Sigma consulting from ClarityArc combines proven methodologies to streamline your operations, minimize defects, and foster a culture of continuous improvement. Whether you're aiming to cut costs, enhance quality, or scale efficiently, our experts guide you every step of the way.
Contact us to learn more about our process advisory services:
Why Lean and Six Sigma are Essential.
In today's competitive landscape, businesses can't afford inefficiencies. Lean focuses on eliminating waste—unnecessary steps, delays, and overproduction—while Six Sigma targets variation and defects to ensure consistent, high-quality outcomes. Together, Lean Six Sigma drives measurable results: reduced costs, faster cycle times, and improved customer satisfaction.
Without these practices, organizations face hidden risks like process bottlenecks, quality issues, and scalability challenges. Our clients in industries like manufacturing, healthcare, and finance have seen up to 30% efficiency gains after implementation. This methodology isn't just a tool—it's foundational for digital transformation, compliance, and long-term growth. By adopting Lean Six Sigma, you empower your teams to make data-driven decisions, turning operational challenges into competitive advantages.
Cut operational costs by identifying waste
Improve quality with statistical analysis
Scale operations confidently
Automate tasks to reduce errors
What we do. Our Lean & Six Sigma Services
At Clarity Arc, we deliver tailored Lean Six Sigma consulting to fit your unique needs. We start with a thorough assessment of your current processes, using tools like Value Stream Mapping and DMAIC (Define, Measure, Analyze, Improve, Control) to pinpoint inefficiencies.
Contact us to learn more about our process advisory services:
Integration & Automation
Prepare your processes for RPA, AI and hyper-automation by ensuring lean foundations.
Implementation
From pilot projects to enterprise-wide rollouts, we provide coaching, tools and metrics tracking for any process or area.
Process Optimization
Facilitated sessions to redesign workflows, reduce errors, improve cycle-times and eliminate non- value added activities.
Training
Hands-on workshops for Yellow, Green and Black Belt levels to equip your team with practical skills and prepare for certification.
We work non-disruptively, collaborating with your subject matter experts (SMEs) to validate changes and ensure buy-in. Aligned with standards like ISO 9001, ASQ guidelines, and industry best practices, our approach guarantees sustainable results.
What you get. Deliverables & Outcomes
Our Lean Six Sigma engagements provide actionable, editable deliverables that integrate seamlessly into your systems. Expect:
Detailed Process Maps: Visual representations in BPMN or swimlane formats, highlighting waste and improvement opportunities.
Data-Driven Reports: Statistical analyses, root cause investigations (e.g., Fishbone diagrams), and performance metrics like sigma levels.
Improvement Roadmaps: Prioritized action plans with estimated ROI, timelines, and responsibility assignments (RACI matrices).
Training Materials and SOPs: Customized standard operating procedures, e-learning modules, and certification pathways.
Ongoing Support Options: Post-project audits, kaizen events, and metrics dashboards for continuous monitoring.
Clients report tangible benefits, such as a 25% reduction in defects for a manufacturing firm or $2M annual savings in healthcare operations. All deliverables are client-owned, secure, and compliant with regulations like HIPAA or FDA standards where applicable.
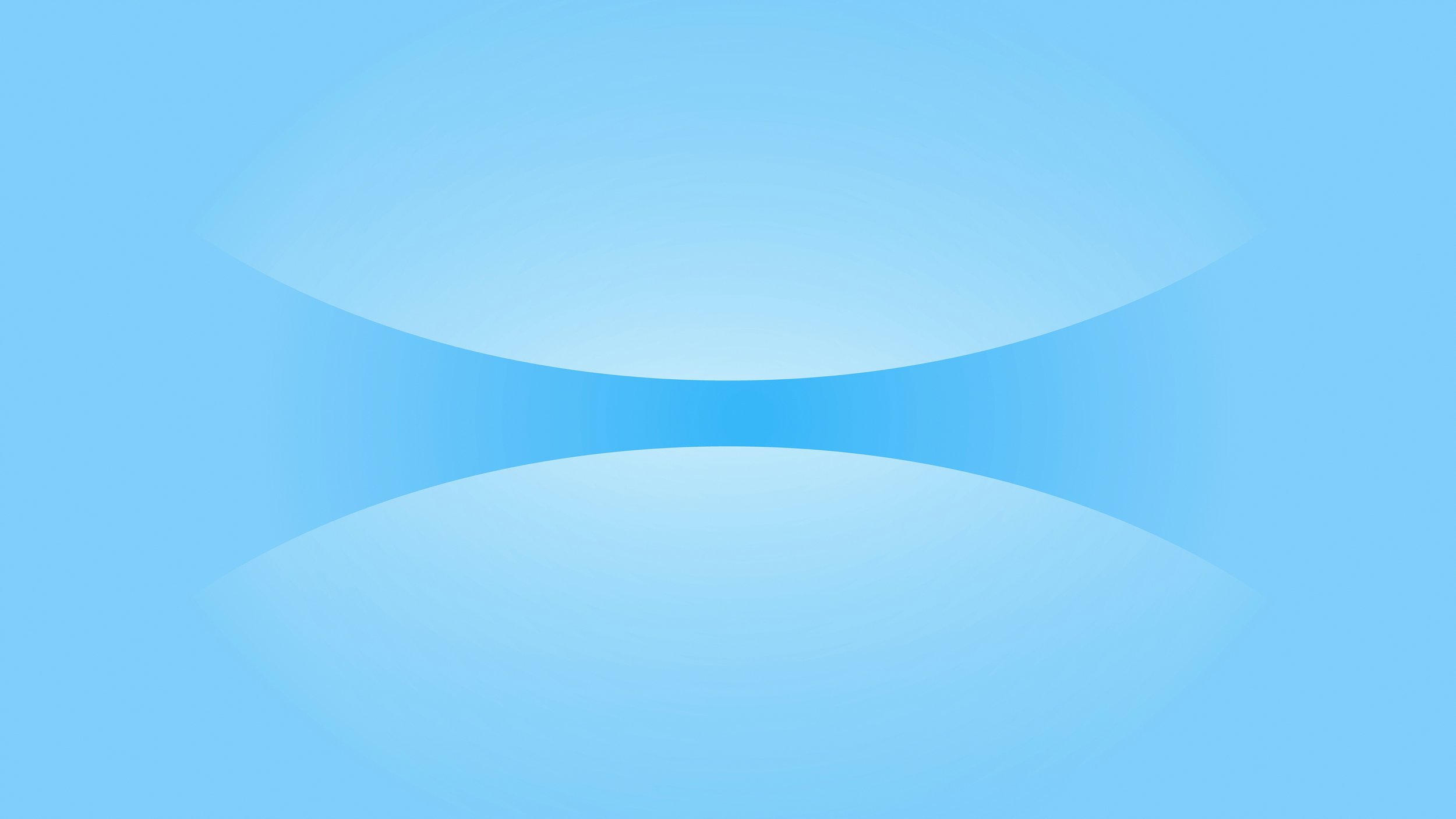
A Typical Lean Six Sigma Project
Our projects are structured for efficiency, typically spanning 4-12 weeks depending on scope. Phases include:
Define and Measure (Weeks 1-2): Scope the project, gather baseline data, and map current processes via interviews and observations.
Analyze and Improve (Weeks 3-6): Identify root causes, brainstorm solutions, and pilot changes using Lean tools like 5S or Kanban.
Control and Handoff (Weeks 7+): Implement controls, train teams, and deliver final reports with sustainment plans.
Case Studies:
Tech Firm: Reduced software deployment time by 50%, saving $1.5M annually.
Logistics Company: Eliminated 15% waste in supply chain, boosting on-time delivery to 98%.
Ready to start? Contact us to discuss your needs.